Construction and engineering machinery operate in demanding environments that require robust, reliable, and efficient braking solutions.
Cranes
Application Scenarios
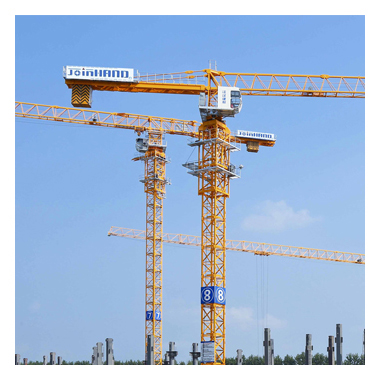
Tower cranes
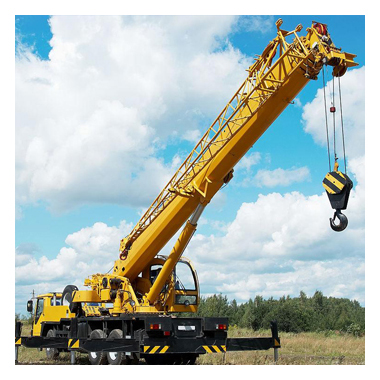
Mobile cranes
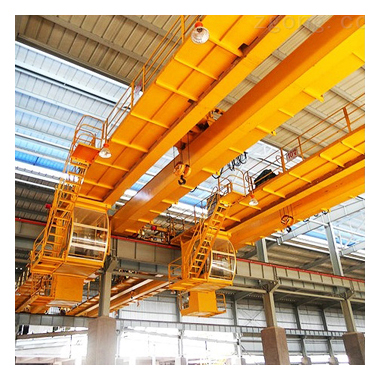
Overhead cranes
Solutions:
High-torque Hydraulic Brakes: Provide strong and consistent braking force for heavy lifting operations, ensuring precise and safe load handling.
Electromagnetic Brakes: Suitable for crane hoisting mechanisms, offering reliable and precise control for both lifting and lowering operations.
Emergency Braking Systems: Essential for ensuring the safety of crane operations, these systems provide quick and reliable stopping power in emergency situations.
Maintenance-friendly Brakes: Designed for easy access and quick replacement of parts, minimizing downtime and maintaining continuous operation.
Excavators and Bulldozers
Application Scenarios
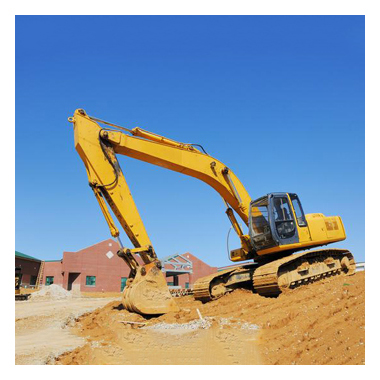
Excavation
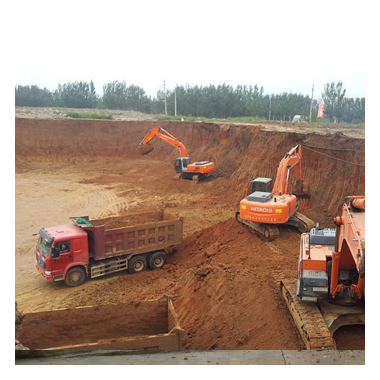
Earthmoving
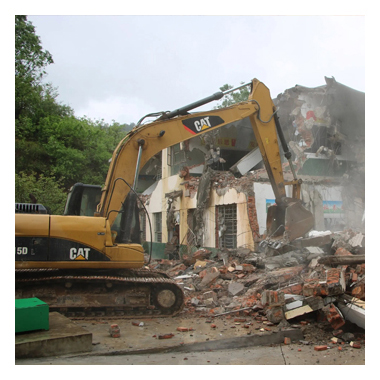
Demolition
Solutions:
Heavy-duty Disc Brakes: Provide reliable braking force for the heavy-duty operation of excavators and bulldozers, ensuring safety on steep and uneven terrain.
Hydraulic Drum Brakes: Suitable for bulldozers, offering robust and consistent braking performance under heavy loads and extreme conditions.
Dust-proof and Water-resistant Brakes: Designed to operate effectively in dusty and wet conditions commonly found on construction sites, extending the lifespan and reducing maintenance frequency.
Regenerative Braking Systems: Capture braking energy to improve efficiency and reduce fuel consumption, particularly useful in hybrid construction machinery.
Loaders and Backhoes
Application Scenarios

Loading and unloading materials
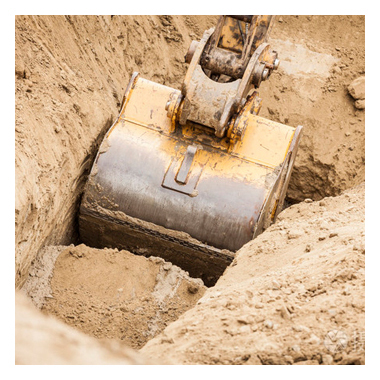
Digging and trenching
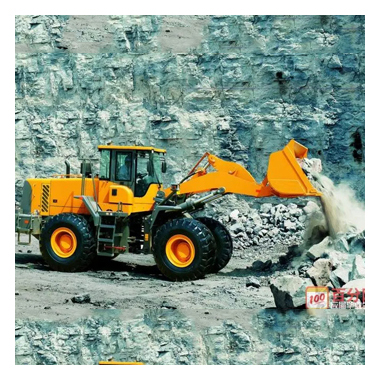
Material handling
Solutions
High-performance Hydraulic Brakes: Provide reliable and strong braking force for loaders and backhoes, ensuring precise control during material handling and digging operations.
Compact Disc Brakes: Suitable for compact loaders and backhoes, offering efficient braking in a compact design that fits within tight spaces.
Multi-disc Brakes: Provide enhanced braking performance for backhoes, ensuring reliable operation in demanding construction environments.
Automatic Brake Systems: Enhance operator safety by automatically applying brakes when the machine is not in use or during idle periods.
Road Construction Equipment
Application Scenarios
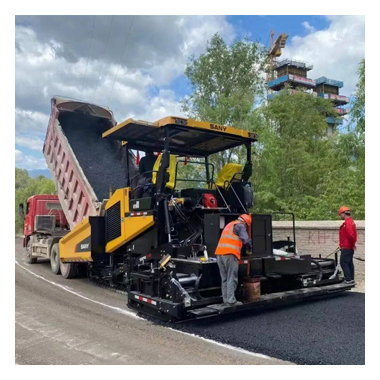
Pavers
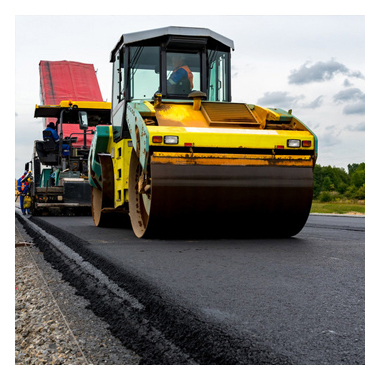
Rollers
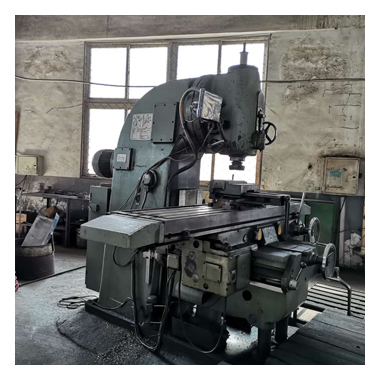
Milling machines
Solutions
Hydraulic Brakes: Offer consistent and reliable braking for road construction equipment, ensuring smooth and safe operation during paving and rolling.
Electromagnetic Brakes: Suitable for milling machines, providing precise control and stopping power to handle the high precision required in road construction.
Emergency Braking Systems: Essential for ensuring safety, these systems provide rapid and reliable braking in emergency situations, protecting operators and equipment.
Wear-resistant Brakes: Designed to withstand the abrasive conditions of road construction, ensuring long-term reliability and reduced maintenance needs.
Concrete and Cement Equipment
Application Scenarios
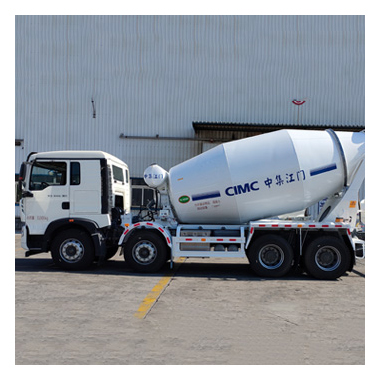
Concrete mixers
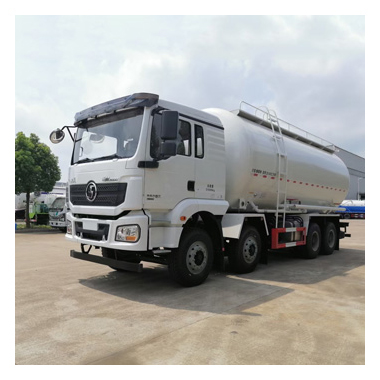
Cement trucks
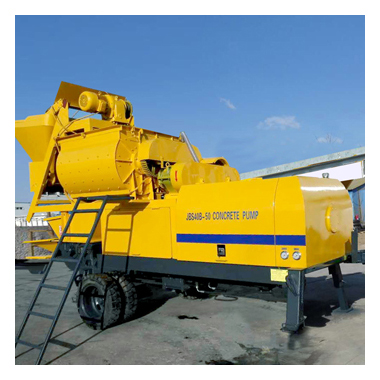
Concrete pumps
Solutions
Heavy-duty Hydraulic Brakes: Provide strong and reliable braking force for concrete mixers and cement trucks, ensuring safe operation under heavy loads.
Drum Brakes: Suitable for concrete pumps, offering robust and consistent braking performance to handle the demanding conditions of concrete delivery.
Dust-resistant Brakes: Designed to operate effectively in dusty environments, extending the lifespan of the brakes and reducing maintenance frequency.
Automatic Brake Systems: Enhance operator safety by automatically applying brakes when the equipment is not in use or during idle periods.
Conclusion
Providing tailored braking solutions for construction and engineering machinery requires a comprehensive understanding of the specific demands and environmental conditions of these sectors. By offering efficient, reliable, and durable braking systems, we can ensure the safety and stability of various construction operations, supporting the industry’s goal of maintaining continuous and safe production. Comprehensive after-sales services further enhance the long-term reliability and performance of these critical systems.
Implementation Steps

Communicate thoroughly with clients to understand specific application scenarios and braking requirements.
Assess environmental conditions, such as seawater corrosion, high humidity, and high salinity.

Design suitable braking systems based on the needs and environmental conditions.
Determine materials, braking methods, and control systems.

Manufacture the brakes according to the design plan, ensuring quality and performance.
Conduct rigorous testing under actual use environments to ensure the reliability and safety of the braking system.

Ensure the system operates normally and provide necessary technical support.

Provide regular maintenance and upkeep services to ensure long-term stable operation of the braking system.
Respond promptly to client repair and replacement needs, offering technical support and training.
Please submit the product requirements and we will contact you immediately