Industrial disc brakes are essential components in various heavy-duty applications, ranging from manufacturing machinery to wind turbines and mining equipment. The choice of materials used in the construction of industrial disc brakes significantly influences their performance, durability, and efficiency. This article explores the materials commonly used in industrial disc brakes, focusing on their properties and benefits.
Understanding Industrial Disc Brakes
Industrial disc brakes function similarly to those in automotive applications, utilizing calipers to apply friction to a rotor or disc to slow down or stop motion. However, industrial disc brakes are designed to withstand more demanding environments and heavier loads. The materials used in their construction must meet stringent requirements for strength, heat resistance, and durability.
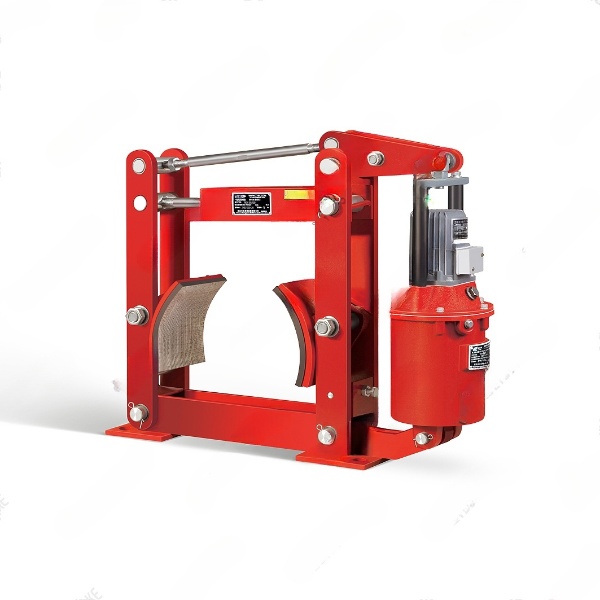
Materials Used in Industrial Disc Brake Rotors
1. Cast Iron
Cast iron is a prevalent material for industrial disc brake rotors due to its robust properties:
- High Thermal Stability: Cast iron can endure high temperatures generated during heavy braking without warping or losing structural integrity.
- Durability: It offers excellent wear resistance, making it suitable for long-term use in industrial settings.
- Cost-Effectiveness: Cast iron is relatively affordable, providing a balance between performance and cost.
2. Steel
Steel, particularly alloy steel, is another common material for industrial brake rotors:
- Strength: Steel rotors can handle higher stress levels and are less likely to crack under extreme conditions.
- Heat Dissipation: Alloy steel has good thermal conductivity, helping to manage the heat produced during braking.
- Corrosion Resistance: Certain steel alloys include elements like chromium to enhance resistance to corrosion, essential for harsh industrial environments.
3. Stainless Steel
Stainless steel rotors are used in applications where corrosion resistance is crucial:
- Corrosion Resistance: Stainless steel is highly resistant to rust and corrosion, making it ideal for environments exposed to moisture and chemicals.
- Longevity: The durability of stainless steel extends the lifespan of the rotors in aggressive conditions.
- Low Maintenance: Stainless steel requires less maintenance compared to other materials, reducing downtime and operational costs.
Materials Used in Industrial Brake Pads
1. Semi-Metallic
Semi-metallic brake pads are widely used in industrial applications due to their robust performance:
- Durability: These pads are made from a combination of metals, such as steel and copper, which provide high durability.
- Heat Tolerance: Semi-metallic pads can withstand high temperatures and dissipate heat effectively, preventing brake fade.
- Performance: They offer consistent braking performance, even under heavy loads and frequent use.
2. Sintered Metal
Sintered metal pads are another popular choice for industrial disc brakes:
- High Strength: Sintered metal pads are made by fusing metallic particles under high pressure and temperature, resulting in a very strong material.
- Wear Resistance: These pads have excellent wear resistance, making them suitable for demanding applications.
- Thermal Stability: Sintered metal pads perform well under extreme temperatures, ensuring reliable braking.
3. Organic
Organic brake pads, also known as non-asbestos organic (NAO) pads, are used in certain industrial applications:
- Noise Reduction: Organic pads are generally quieter than their metallic counterparts, which can be beneficial in noise-sensitive environments.
- Eco-Friendly: These pads do not contain asbestos and are made from materials like rubber, glass, and resins, making them safer for the environment.
- Smooth Braking: Organic pads provide smooth and gradual braking, which can be advantageous in specific industrial settings.
Conclusion
The materials used in industrial disc brakes are selected to meet the rigorous demands of various heavy-duty applications. Cast iron and different types of steel are common choices for rotors due to their strength, heat resistance, and durability. For brake pads, semi-metallic and sintered metal options offer high performance and wear resistance, while organic pads provide quieter and smoother operation. Understanding the materials behind industrial disc brakes is crucial for selecting the right components to ensure safety, efficiency, and longevity in industrial environments.
Implementation Steps

Communicate thoroughly with clients to understand specific application scenarios and braking requirements.
Assess environmental conditions, such as seawater corrosion, high humidity, and high salinity.

Design suitable braking systems based on the needs and environmental conditions.
Determine materials, braking methods, and control systems.

Manufacture the brakes according to the design plan, ensuring quality and performance.
Conduct rigorous testing under actual use environments to ensure the reliability and safety of the braking system.

Ensure the system operates normally and provide necessary technical support.

Provide regular maintenance and upkeep services to ensure long-term stable operation of the braking system.
Respond promptly to client repair and replacement needs, offering technical support and training.
Please submit the product requirements and we will contact you immediately